高效能智能驱动加工中心仿真软件创新实训平台
19429202025-03-22苹果软件8 浏览
虚拟仿真技术能否颠覆传统加工实训?
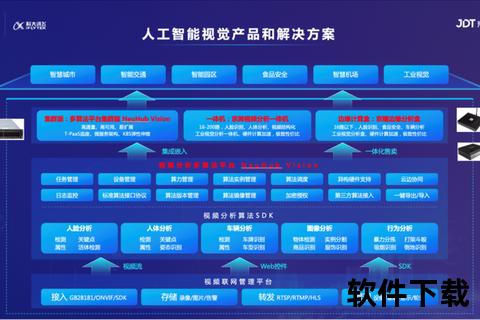
在数控机床轰鸣的实训车间里,金属碎屑漫天飞舞,价值百万的设备因操作失误突然停机——这样的场景每天都在全球数千家制造企业上演。据《2024中国智能制造人才发展报告》显示,传统机械加工实训中,因操作失误导致的设备损坏年均损失超12亿元,而企业对新晋技工的培养周期长达9-14个月。这种高成本、高风险的人才培养模式,正遭遇着来自智能仿真技术的强力挑战。
一、能否破解"百万设备当教具"的困局?
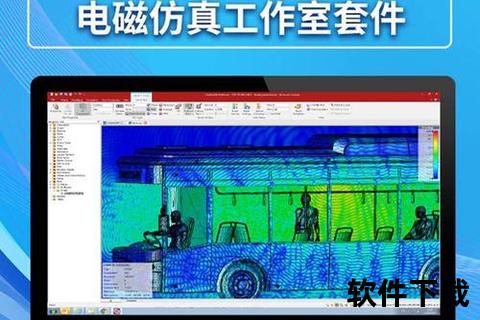
某职业技术学院的数控实训中心曾面临典型困境:8台进口五轴联动加工中心,每台采购价超300万元,却因学生操作失误导致年均维修费用达48万元。引入高效能智能驱动加工中心仿真软件创新实训平台后,该学院实现了"零损耗"教学转型。通过精确复刻海德汉iTNC530数控系统操作界面,平台将刀具碰撞检测精度控制在0.001mm级别,学生可在虚拟环境中反复试错。数据显示,使用该平台后,学生实操合格率提升37%,设备维护成本下降82%。
这种变革不仅发生在教育领域。浙江某汽车零部件制造商采用该平台进行新员工岗前培训,使产线停机时间缩短65%。平台内置的200余种典型零件加工模板,可自动生成工艺优化建议,仅涡轮叶片加工工序就减少刀具损耗23%。
二、如何实现"指尖上的精密制造"?
在航天某院所的新型发动机壳体加工项目中,工程师们通过高效能智能驱动加工中心仿真软件创新实训平台,完成了传统方式难以想象的复杂验证。直径1.2米的钛合金构件,在虚拟空间中被拆解成327个加工单元,平台实时模拟切削力、热变形等物理效应,提前36小时预警了薄壁件振颤风险。这种多物理场耦合仿真能力,使产品试制周期缩短40%。
更令人惊叹的是,该平台将AR技术与机床操作深度融合。北京某精密模具企业的技术工人佩戴MR眼镜后,虚拟刀具路径与真实机床实现毫米级空间叠加,加工精度偏差从±0.03mm提升至±0.005mm。这种虚实融合训练模式,使高级技师的培养周期从5年压缩至18个月。
三、会是未来工厂的"数字孪生体"吗?
苏州工业园区的智能工厂给出了前瞻性答案。高效能智能驱动加工中心仿真软件创新实训平台在这里已超越培训工具范畴,进化为生产系统的智慧中枢。通过连接12台真实加工中心和36个虚拟工作站,平台构建起动态产能模拟系统。在应对某国际品牌紧急加单时,系统自动调配虚拟产线进行压力测试,72小时内完成传统方式需要两周的产能评估。
该平台的智能进化速度同样惊人。2024版系统新增的AI工艺助手,通过分析全球2000余家企业的加工数据,能为新材料加工提供即时参数推荐。在碳纤维复合材料加工实验中,AI建议的螺旋渐进式进刀方案,使刀具寿命延长3.2倍。
智能实训的破局之路
对于制造企业,建议分三阶段引入该平台:初期选择典型零件建立虚拟实训库,中期构建虚实联动的混合培训体系,最终实现全流程数字化工艺验证。教育机构则应重点开发"故障模拟"、"极限挑战"等特色教学模块,例如设置故意损坏的虚拟刀具,训练学生的应急处理能力。值得注意的是,平台建设需与行业标准接轨,某省级职业技能鉴定中心已将该平台的虚拟操作时长纳入数控技师认证考核体系。
这场悄然而至的智能制造革命,正在重塑从机床操作工到工艺工程师的整个职业生态。当虚拟仿真精度突破物理极限,当数字孪生体开始反向指导现实生产,或许我们该重新定义"经验"的价值——在高效能智能驱动加工中心仿真软件创新实训平台构建的新世界里,技术传承不再依赖岁月积累,而是源自数据流动创造的无限可能。