创新智能机械工程师软件高效赋能未来工业新纪元
19429202025-03-24最新更新8 浏览
当传统制造业遇上智能革命:创新软件是“救星”还是“花瓶”?
在工业4.0浪潮下,一个尖锐的问题摆在眼前:当生产线上的老师傅还在用图纸和扳手“驯服”机器时,那些号称能“一键优化”的智能软件,究竟是推动工业升级的真利器,还是资本炒作的空中楼阁?
三年前,某知名汽车零部件厂耗资千万引入智能设计平台,却因工程师操作困难导致系统闲置;而另一家小型机械厂仅用30万元的国产软件,实现了加工效率提升40%。这种反差揭示了一个核心矛盾:创新智能机械工程师软件高效赋能未来工业新纪元的目标虽好,但关键在于如何让技术真正“落地生根”。
1. 智能软件能否破解复杂工艺难题?
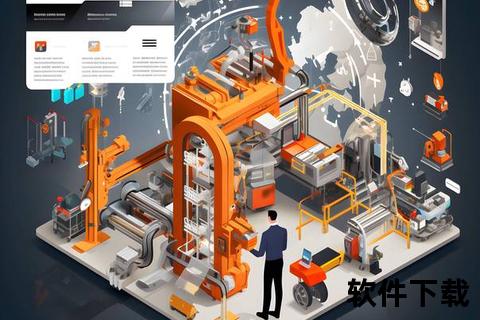
在浙江某液压阀制造厂,工程师曾为0.01毫米的密封面精度夜不能寐。传统加工需反复试切20次以上,而引入Autodesk Inventor 2020的参数化设计系统后,通过自适应算法自动优化刀具路径,将试切次数降至3次。该软件的数字孪生功能更将故障率从12%压至2.8%,印证了创新智能机械工程师软件高效赋能未来工业新纪元的实际价值。
更具突破性的是山东某工程机械企业的实践。面对挖掘机铲斗角度调整的世界级难题,他们利用ANSYS拓扑优化软件,结合金属3D打印技术,创造出仿生蜂窝结构铲斗。这种“软件定义硬件”的模式,使设备寿命延长2.3倍,能耗降低18%。数据显示,采用智能设计软件的企业,新产品研发周期平均缩短47%,验证了软件对复杂工艺的降维打击能力。
2. 数据互联如何重构生产逻辑?
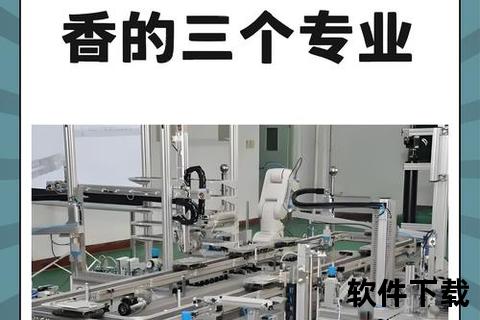
苏州某智能仓储企业的蜕变极具说服力。过去其物流分拣错误率高达8%,引入欧姆龙PLC+IoT解决方案后,通过边缘计算实时处理10万级传感器数据,使分拣准确率达到99.997%。更惊人的是,系统能根据历史数据预测设备故障,提前72小时发出预警,将停机损失从年均300万元压缩至15万元。
在北京某数控机床厂,工程师借助TwinCAT软件平台,实现了“数据驱动刀具”的革命。通过采集切削过程的振动、温度等150项参数,系统自主调整进给速度,使刀具寿命从500件/把提升至2200件/把。这种从“经验主导”到“算法决策”的转变,正是创新智能机械工程师软件高效赋能未来工业新纪元的核心体现。
3. 人机协同会取代工程师吗?
深圳某无人机企业的实践给出辩证答案。其旋翼装配曾高度依赖技师手感,良品率波动在75-85%之间。引入增强现实辅助系统后,新手工程师佩戴AR眼镜即可获得实时装配指引,使培训周期从6个月缩短至2周,良品率稳定在98%以上。这证明智能软件不是替代工程师,而是将人力从重复劳动中解放,聚焦创造性工作。
更具前瞻性的是重庆某汽车工厂的“AI学徒”计划。通过将老师傅的调试经验编码为机器学习模型,系统可自主完成80%的设备参数调校。但关键决策仍需人工审核,形成“AI建议-人类决策”的协同模式。这种“数字工匠”与人类智慧的共生关系,预示着创新智能机械工程师软件高效赋能未来工业新纪元的终极形态——不是机器取代人,而是人机共进化。
破局之道:让技术回归工具本质
对于企业决策者,建议实施“三步走”策略:
1. 选择性嫁接:优先在质检、运维等数据密集型环节引入软件,如某轴承厂通过视觉检测软件将漏检率从0.5%降至0.02%
2. 人才再造:建立“软件+工艺”双导师制,某阀门企业通过内部认证体系,使56%的老技师转型为数字化工程师
3. 生态共建:加入工业软件开源社区,某机床厂通过贡献加工算法,获得20余家上下游企业的数据共享权益
当智能软件褪去炒作光环,回归“工程师的智能扳手”本质时,我们终将看到:那些流淌着代码与数据的生产线,不是冰冷的机器替代,而是人类工业文明的新火种。正如德国工业4.0之父Kagermann所言:“最好的工厂,是让最普通的工人也能施展出大师级技艺的地方”——这正是创新智能机械工程师软件高效赋能未来工业新纪元的终极使命。