创新驱动高效赋能工业仿真软件开启智慧制造新纪元
19429202025-03-25最新更新9 浏览
工业仿真软件:智慧制造的「破局者」还是「空中楼阁」?
当特斯拉上海工厂因冲压工艺误差损失超2亿元时,人们猛然发现——即便在工业4.0时代,制造业仍困于数据迷雾与物理规律的博弈。传统经验主义在复杂工艺面前频频失效,而进口仿真软件高达80%的市场垄断率,更让中国制造面临「卡脖子」风险。争议随之而来:在算法壁垒高筑、巨头环伺的战场,国产工业仿真软件能否撕开突破口?创新驱动高效赋能工业仿真软件开启智慧制造新纪元,究竟是技术理想还是触手可及的未来?
一、核心技术突破:物理规律能否被AI重新定义?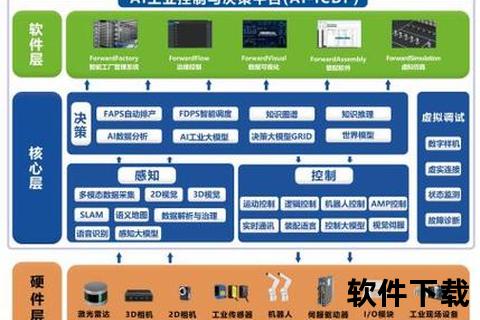
工业仿真的本质,是将现实世界的物理规则转化为可计算的数字模型。过去三十年,有限元分析、流体力学等核心算法框架早已固化,而AI技术的介入正在颠覆这一格局。华为云数字孪生平台通过「AI+多物理场仿真」技术,在汽车焊接工艺中预测热变形误差,使良品率提升12%。这种突破源于对传统算法的重构:AI不仅加速了海量工况数据的解析,更通过自学习机制优化了模型精度。
更激进的变革发生在凡拓数创的FTE引擎中。该平台将300多个工业机理模型与自研「智造大模型」融合,实现从仿真到决策的闭环。在某航空零部件工厂,系统通过模拟不同切削参数的应力分布,将刀具寿命延长20%,材料损耗降低15%。这种「物理AI」模式,本质是通过数据反哺理论,让算法在真实生产场景中持续进化。
二、国产替代路径:如何跨越「能用」到「好用」的鸿沟?
英特仿真的突围轨迹颇具代表性。这家深耕CAE领域15年的企业,通过与三一重工、长城汽车等头部厂商的深度绑定,在工程机械液压系统仿真领域实现进口替代。其INTESIM-MultiSim平台的多场耦合精度达到国际标准的98%,而成本仅为国外同类产品的60%。这种「行业定制+场景验证」的模式,正在打破「国产软件只能做教学演示」的偏见。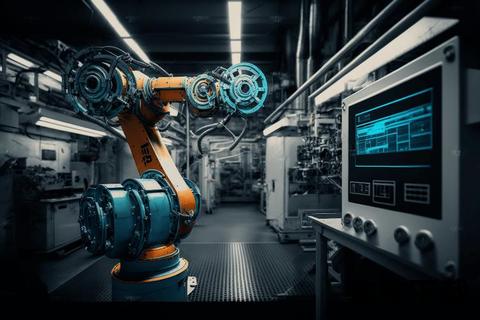
2024年宁波舟山港的实践更具说服力。阿里云DataV Twin平台以轻量化渲染技术,将320万平方米集装箱场景的数字化还原资源消耗降低90%,同时实现秒级路网仿真响应。这种技术迭代并非单纯模仿,而是抓住「实时性」和「规模化」两大痛点,在港口调度、交通管理等场景建立起差异化优势。
三、生态构建:单点技术如何裂变为产业革命?
工业仿真的真正价值,在于打通从设计到运维的全链路。海克斯康打造的「工业互联网+智能制造」生态,覆盖产品全生命周期,其虚拟调试技术帮助某家电企业将产线调试周期从3个月压缩至2周。这种生态化能力,本质是通过仿真数据流串联起离散的工业环节。
更具前瞻性的实践来自IPS智参科技的AIPLANT平台。该系统的「五级建模体系」实现了从企业级战略到设备级参数的穿透式管理,在蔚来汽车工厂中,通过实时映射人机交互与物料流转数据,使远程故障诊断响应时间缩短60%。这种「数字主线」思维,正将仿真技术从工具升级为制造系统的「神经中枢」。
破局之道:从技术攻坚到价值重构
创新驱动高效赋能工业仿真软件开启智慧制造新纪元,需要三条行动路径:
1. 场景反哺研发:借鉴华为云与汽车厂商的联合实验室模式,以真实生产数据训练算法模型,建立「问题发现-技术攻关-应用验证」的闭环链条。
2. 生态协同破壁:参照海克斯康的产业联盟机制,推动仿真软件商、设备制造商、云服务商共建标准接口与数据协议,解决「信息孤岛」难题。
3. 人才梯度培育:学习英特仿真与高校联合培养硕博的模式,构建「工业机理专家+算法工程师+行业顾问」的复合型团队,弥合理论与实践的断层。
当国产仿真软件在特斯拉工厂替代进口方案时,一个更具启示性的事实浮现:这场技术突围的本质,是对制造本质的重新认知——唯有将物理规律、数据智能与产业需求熔铸为新的方法论,才能真正打开智慧制造的「中国方案」。创新驱动高效赋能工业仿真软件开启智慧制造新纪元,此刻已不仅是愿景,而是正在发生的产业革命。