智能革新工厂管理软件全方位驱动企业卓越效能升级
19429202025-03-23电脑软件13 浏览
一、传统工厂管理为何频频遭遇瓶颈?
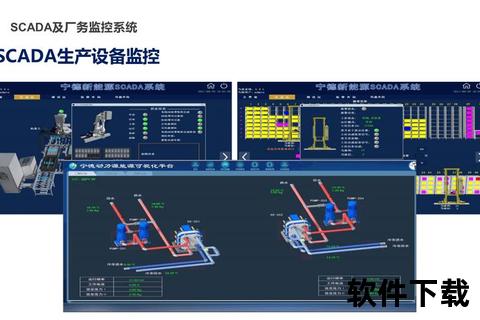
当一家年产值数亿元的汽车零部件工厂,因人工记录生产数据导致订单延误时;当某纺织企业因无法追溯质量问题而损失千万级客户时——这些并非虚构情节,而是中国制造业数字化转型前夜的真实写照。据国家统计局数据,我国44%的制造企业面临招工难题,而采用智能管理系统的企业生产效率平均提升超30%。在人力成本攀升与质量要求严苛的双重压力下,智能革新工厂管理软件全方位驱动企业卓越效能升级,正成为破解困局的关键钥匙。
二、智能工厂能否真正实现“无人化”生产?
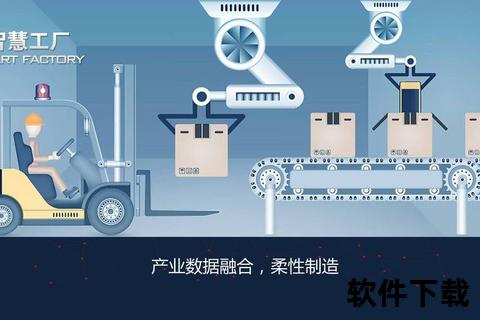
北京亦庄的小米黑灯工厂给出了震撼答案:200个高清摄像头与8000多个传感器构建的神经网络,让手机主板贴片等200多道工序实现24小时无人值守,生产效率较人工提升25%。这背后是MES(制造执行系统)与ERP(企业资源计划)的深度耦合:前者实时采集设备状态、良品率等3000余项数据,后者则动态调整物料供应与订单排期。
苏州友成机工的实践更具普适性。通过部署数智化管理系统,该企业实现了注塑成型周期缩短18%、设备利用率提升22%的突破。其智能决策模块运用机器学习算法,可提前48小时预警设备故障,将非计划停机减少70%。这些案例印证,智能革新工厂管理软件全方位驱动企业卓越效能升级,已从概念验证进入规模化应用阶段。
三、数据孤岛如何转化为决策金矿?
湖南钢铁集团的蜕变极具说服力:通过5G专网连接2.6万台设备,构建的数字孪生系统可实时模拟高炉工况,使吨钢能耗降低8%,年节约成本2.5亿元。其核心在于工业大数据平台,能对炼钢过程的1200多个参数进行毫秒级分析,将工艺优化周期从3个月压缩至72小时。
在半导体领域,格创东智研发的CIM系统更颠覆传统——通过自研的T-work平台,将韩国进口系统的响应速度提升5倍,良率分析精度达99.97%。该系统独创的动态知识图谱技术,可自动生成200+维度的质量分析报告,使工程师决策效率提升60%。这些数据价值的深度挖掘,正是智能革新工厂管理软件全方位驱动企业卓越效能升级的核心动能。
四、中小型企业如何跨越数字化鸿沟?
广东某纺织厂的转型故事颇具启示:原依赖纸质工单的车间,引入云端MES后实现生产可视化,订单交付周期从45天缩短至28天,客户投诉率下降52%。该系统提供模块化配置,初期投入仅需传统方案的1/3,特别适合多品种小批量生产模式。
对于微型工厂,山海鲸可视化工具开创零成本转型路径。某五金加工厂借助其拖拽式界面,3天即完成设备联网,通过能耗热力图发现空压机群组存在30%的无效能耗。这种轻量化工具的出现,使得数字化不再是龙头企业的专属特权。
五、智能革命的下一站路标指向何处?
当KUKA的协作机器人开始自主优化焊接路径,当数字孪生技术能预判未来72小时的生产波动,制造业的竞争已进入「预测性智造」新纪元。企业可遵循三个实施原则:
1. 分步渗透:从设备联网等基础模块切入,参考湘钢「设备开口说话」的实践路径
2. 生态共建:选择支持API接口的ERP系统,如用友U9 cloud可对接150+工业APP
3. 人才反哺:建立数字化培训体系,某汽车配件厂通过「数字导师」计划,使一线员工数据分析能力提升400%
这场由智能软件引领的制造业革命,绝非简单的机器换人,而是通过数据流重构价值链条。那些率先完成智能革新工厂管理软件全方位驱动企业卓越效能升级的企业,正在书写中国智造的新范式——在这里,每个传感器都是利润增长点,每串代码都在重塑产业竞争力。