高效赋能智能制造新时代的CAXA软件革新之道
19429202025-03-24电脑软件8 浏览
一、传统制造转型之困:技术瓶颈如何突破?
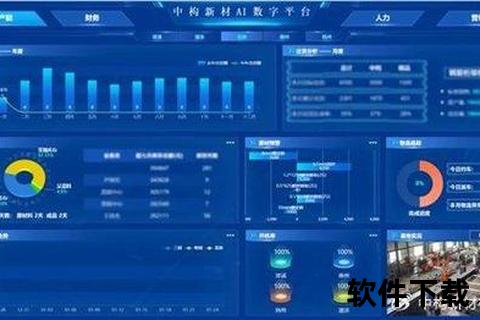
在智能制造浪潮下,中国制造业面临着"数字鸿沟"的尴尬:一边是头部企业利用工业软件实现设计效率翻倍增长,另一边却是大量中小企业因软件功能割裂、操作复杂而深陷"数据孤岛"。当某阀门企业耗时3个月仍无法完成复杂管路的数字化建模时,CAXA 3D实体设计2025的管路模块仅用3天就解决了这一难题。这种效率断层背后,折射出传统工业软件在智能化转型中的核心矛盾——如何将专业功能与用户实际需求精准对接?
CAXA的破局之道在于"场景化创新"。其2025版本新增的100多项功能中,80%直接针对装备制造、零部件加工等场景痛点。例如在大型结构件设计中,工程师过去需要手动标注数百个焊接参数,而CAXA 3D 2025的组焊件模块可自动生成BOM清单,使某起重机厂商的设计周期缩短40%。更值得关注的是AI技术的深度植入:当某汽配企业面对海外客户提供的PDF图纸束手无策时,CAXA电子图板的AI识别功能实现了图纸数据秒级解析,将传统需要2周的手工绘图压缩至2小时。这些案例印证了:技术革新必须扎根于产业实际需求。
二、数据孤岛破除术:全链条协同何以实现?
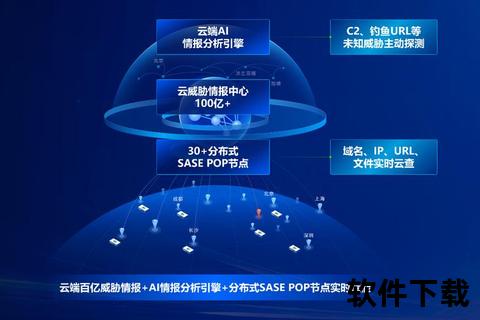
沈阳某航空零部件制造厂曾陷入典型的数据困境:设计部门用CAD完成的模型,工艺部门需要重新建模,车间数控机床又要再次编程。这种"三张皮"现象导致产品交付周期长达6个月。CAXA的解决方案是从底层架构打破壁垒,其PLM系统将设计(CAD)、工艺(CAPP)、制造(CAM)数据流贯通,使该企业实现从图纸到G代码的自动转化,交付周期锐减至45天。
这种协同能力的核心在于MES系统的进化。2024版CAXA MES通过微服务架构重构,支持2000台设备并发接入,在西航集团的实践中,实现了车间设备数据采集速度从分钟级提升至毫秒级。更突破性的是云端协同能力:当新冠疫情导致某水泵企业德国专家无法现场指导时,CAXA的云平台支持中德两地工程师同步进行装配体参数化调整,使新产品试制周期逆势缩短30%。数据表明,采用CAXA全链条解决方案的企业,跨部门协作效率平均提升57%。
三、行业赋能密码:通用平台如何适配个性需求?
在浙江某民营锁具企业的数字化进程中,管理层曾陷入两难:既需要适合小批量定制化生产的柔性系统,又受限于200万元的预算。CAXA给出的答案是"积木式"解决方案——通过PLM标准模块+五金行业套件的组合,仅用68万元就实现了从订单到交付的全流程数字化,使该企业接单能力提升3倍。这种"标准+定制"的模式,正是CAXA深耕30余年形成的独特优势。
不同行业的实践印证了这种柔性适配能力:在航空领域,CAXA CAPP 2025的动态表格功能,解决了某主机厂万级工序卡片的智能关联难题;在汽车行业,CAM制造工程师的轨迹优化算法,使某变速箱厂商的刀具损耗率降低22%。教育领域的创新更显前瞻性:与黄河水利职业技术学院共建的数字化实训工厂,将企业真实项目数据植入教学系统,学生毕业即可操作CAXA全链条软件,人才适配度提升90%。这种行业Know-How的沉淀,使CAXA能像"工业安卓"般适配不同制造场景。
通向智造未来的三条实操路径
对于谋求转型的制造企业,建议采取"三步走"策略:首先开展数字化成熟度评估,重点检测设计、工艺、制造环节的数据断点(CAXA提供免费检测工具);其次选择1-2个核心场景试点,如某阀门企业率先在质检环节部署CAXA MES,3个月内实现不良品率下降35%;最后建立持续改进机制,借鉴永生重工经验,通过CAXA在线知识库每月更新技能。
高效赋能智能制造新时代的CAXA软件革新之道,本质是让技术回归工程本质。当某小微企业主用手机就能查看车间实时数据,当老师傅通过AR眼镜获得CAXA系统的装配指引,这些场景正在宣告:智能制造不是巨头专利,而是每个制造单元都能触及的未来。这条路或许仍有坎坷,但CAXA用30年130项专利的积累证明:真正的工业软件革命,永远始于车间,成于生态。